by Jennifer Hart Yim | Oct 22, 2019 | Blog, Current Events, Logistics, Manufacturing & Distribution, Strategy, Supply Chain
Amazon has changed the way we do business. Supply chain companies need to get on board with Amazon’s e-commerce strategy or risk losing business.
It is no secret that Amazon has dominated the online retail industry. Amazon Prime has shifted consumer expectations so that waiting 5-7 business days for your online order is no longer acceptable. With people now ordering anything from couches to groceries online, companies need to get on board with this shift to e-commerce or risk missing out on many sales.
Consumers now more than ever want access to more inventory no matter if they are shopping online or in stores. Many companies report the struggle of trying to keep up with this retail giant, and current-day supply chains have certainly felt the impact.
Historically, supply chains have been set up to support a network of stores using the multichannel business model. This includes retailers managing their different channels almost as separate businesses. These channels are what businesses use to get their goods and services to their consumers. For example, many retailers use brick-and-mortar stores as well as e-commerce when it comes to selling.
So, what’s the problem with this? Well, the customer’s experience can vary depending on the shopping channel they choose. Retailers often keep their online and brick-and-mortar inventory separate, which can lead to a frustrating shopping experience for the customer.
I am sure at some point in your life you have had the experience of walking into a store looking to return an online order only to find out it must be returned to the company through the mail. Customers do not view a brand in silos, and the same selection of inventory is expected whether they are shopping online or in a physical store. Companies also run the risk of losing a sale if the exact item the consumer wants is unavailable or sold out. This is one area that allows Amazon to shine because they maintain one pool of inventory that is not separated by different channels of business.
A 2016 UPS survey found that, for the first time, shoppers revealed they bought more of their purchases online than in stores. It’s hard to tell what is the main driver behind this shift, but you can’t help but think of Amazon. It’s hard to comprehend how other companies not only compete but just even keep up with the trillion-dollar company with a revenue of $10.07 billion in 2018.
This is where the omnichannel business model comes into play. Omnichannel combines physical and online commerce to create a more seamless shopping experience for the consumer. While this business model is not a result of Amazon, it certainly puts companies in a better position to compete. The goal here is to provide the same customer experience throughout each channel while ensuring the product reaches the customer as fast as possible.
Characteristics of an omnichannel business model include:
- Buy online pick up in stores
- Stores shipping to other stores
- Dropshipping
- Order fulfillment from store
Nordstrom finding ways to differentiate from the competition
Online shopping provides many benefits to consumers, but it does not come without its own challenges. It is fairly common to buy a shirt online only to find out it is the wrong size. It can be a hassle to mail the item back, and consumers often opt out of this and chalk the purchase up to a loss. Nordstrom understands this pain point and took it upon themselves to offer a solution by creating service hubs called Nordstrom Local. The sole purpose of Nordstrom Local is to make the online shopping experience effortless. While these hubs do not contain designated inventory, they provide a handful of services to the customers.
They offer:
- Pickups
- Returns
- Stylist
- Dressing rooms
- Tailoring services
- Same-day delivery (if ordered before 2 p.m.)
- Espresso drinks, juices, wine & beer
As a consumer, what more could you ask for? The idea is that you order a variety of clothes online and have them delivered to Nordstrom Local. Here you can try on your purchases in their dressing rooms. If it doesn’t fit, no problem — they’ll mail it back for you. Need it hemmed? There’s a tailor on-site.
Nordstrom has held its own in the retail space. With 2018 revenue reaching $15.5 billion, it is hard to argue with their success. They must continue to innovate and find new ways to connect consumers to their product. Trying out this concept in Los Angeles has proven to be successful, and they are looking at opening up hubs in New York next.
Kohl’s joins forces with Amazon
Kohl’s, like many retail stores, welcomes any opportunity to increase foot traffic. Over 1,000 of their stores are now accepting returns from Amazon. Again, we see a pain point of online shopping removed for the consumer. You can bring your unwanted Amazon item to Kohl’s, and they will pack, label, and ship the item at no cost. The hope is that Amazon customers will flock to Kohl’s and hopefully buy some of their inventory on the way.
Their revenue has continued to rise over the past four years and reached 20 billion in 2018. This is a bold idea that can set Kohl’s apart from the competition by delivering a service that is unique to them. Amazon needs a way to keep its customers happy and Kohl’s needs to increase foot traffic, so it appears to be a win-win for all parties involved — including the consumer.
While Kohl’s new idea offers fewer services than Nordstrom’s, they are opening themselves up to a wider consumer market, and with this will likely come more sales. They have addressed the expected increase in expenses that will come with having to hire more employees and spending more on logistics, but the expected payoff is potentially massive.
Comparing strategies
It’s hard to tell which strategy will prove to be more profitable. The only thing that is for certain is that the shift toward e-commerce is not slowing down anytime soon, so companies need to look at how they connect consumers to their product. If the goal is to get your product to the consumer, then your supply chain needs to be tailored to this objective.
Amazon may have the upper hand now, but you never know what new idea could pop up in a few years. In the meantime, companies are faced with the harsh reality of ever-growing competition. Consumers are now hopping on their computers or mobile devices to choose from a plethora of inventory.
Amazon is not completely to blame when it comes to the evolution of consumer expectations, but they have certainly impacted them. Companies wanting to compete are left to make tough but critical decisions on what their next move will be.
This article was written by Emily Standish, an MBA student at the Peter T. Paul College of Business and Economics at the University of New Hampshire, specializing in Finance and Information Systems & Business Analytics. She graduated from Merrimack College in 2017 with a B.S. in Business Administration and Management with a concentration in Finance and currently works as a Corporate Financial Analyst.
Related posts:
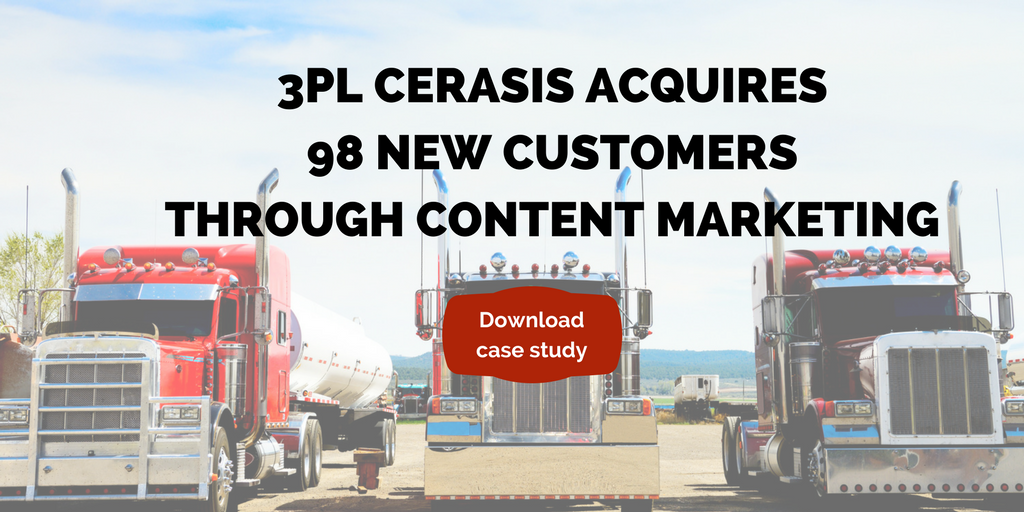
by Fronetics | Sep 3, 2019 | Blog, Current Events, Logistics, Supply Chain
The long-rumored launch of an Amazon logistics service is unlikely to be rumor much longer. Here’s what 3PLs need to know.
Highlights:
- Amazon recently invited select shippers to use a service called Amazon Shipping.
- The retail giant boasts a global logistics footprint that covers 243.5 million square feet – and counting.
- Amazon’s hiring plans offer insights into its plans for logistics services.
Rumors of an Amazon logistics service have been swirling for nearly two years. In February 2018, the Wall Street Journal predicted that Amazon was planning to launch a “delivery service that would vie with FedEx, UPS.”
In April of this year, Amazon re-stoked discussion of its long-rumored logistics service by inviting select shippers in three major U.S. cities to use a service called Amazon Shipping. While more recent reports indicate that this Amazon logistics service may not be attractive to all shippers, it’s time to consider the possibility that Amazon is about to become a player in the logistics sector.
The growth of Amazon Logistics
Shortly before the April 2019 reports surfaced, Amstrong & Associates Inc., a logistics industry research and consulting firm, published a detailed report on Amazon Logistics. Summing up the report’s conclusions, A&A President Evan Armstrong said, “Amazon is acting increasingly like a 3PL.”
Armstrong’s report estimates that Amazon provides logistics services for 12% of B2C shipments worldwide, noting that third-party sellers account for more than half of all units sold through the Amazon platform. Eytan Buchman, vice president of marketing at Freightos, points to Amazon’s massive logistics footprint at 243.5 million square feet.
The network of warehouses and distribution centers that make up Amazon Logistics comprises 386 facilities in the U.S. alone. That includes 159 fulfillment centers, 47 inbound and outbound sortation hubs, 52 Prime Now hubs, and 115 local delivery stations, according to data compiled by Montreal-based research firm MWPVL International.
Amazon CEO Jeff Bezos has often emphasized the importance of “how fast [a product] will ship or be available for pickup,” as in his 2017 letter to shareholders. As evidence of Amazon’s focus on logistics, Buchman points to the company’s 2018 competition assessment, identifying “companies that provide fulfillment and logistics services for themselves” as competition.
Yet experts remain divided when it comes to labeling Amazon outright as a 3PL. Armstrong, for example, doesn’t place Amazon in the same category as 3PLs because logistics “is just part of their business.” On the other hand, Satish Jindel of SJ Consulting Group estimates that Amazon generated $42.5 billion in gross revenue from logistics services worldwide in 2018, making it the world’s leading 3PL.
Hiring plans for Amazon Logistics
In doing a deep dive into the nearly 17,700 full-time vacancies listed on Amazon’s website, Buchman formed some interesting insights into Amazon’s plans. Here are the key points he found:
- 920 (or 5%) of the 17,700 jobs listed are in the logistics and transportation sector.
- About half of these logistics and transportation jobs are in the U.S.
- More than half of the vacancies require at least 4 years’ experience.
- More than 10% require at least 7 years’ experience.
- 14 jobs require more than 10 years’ experience.
Based on his analysis, Buchman believes that it’s “clear exactly where the company is moving – cross-border trade and international logistics, while improving courier delivery.”
What does Amazon Logistics mean for the sector?
The Amazon effect is the subject of much discussion, speculation, and anxiety for manufacturers and distributors, and Amazon Logistics is no exception. Other 3PLs, such as FedEx, have publicly insisted that Amazon poses no threat – despite statements to the contrary from Wall Street analysts.
In contemplating where Amazon logistics leaves other 3PLs, Buchman concludes that while “few operate at the same scope as Amazon’s level of business… most do already have the expertise, physical networks, and internal technological capabilities to differentiate.” He concludes on the relatively gloomy note: “Doubling down on improving user experience had recently become the way to stay ahead. But now, it’s looking like the way not to fall behind.”
At Fronetics, we’ve written before about the challenges that the Amazon effect poses for supply chain and logistics companies – and why it’s ultimately a net positive. Amazon’s disruptions to the sector are likely to continue, and, as they do, the rest of the industry has the opportunity to refine and sharpen its practices.
Related posts:
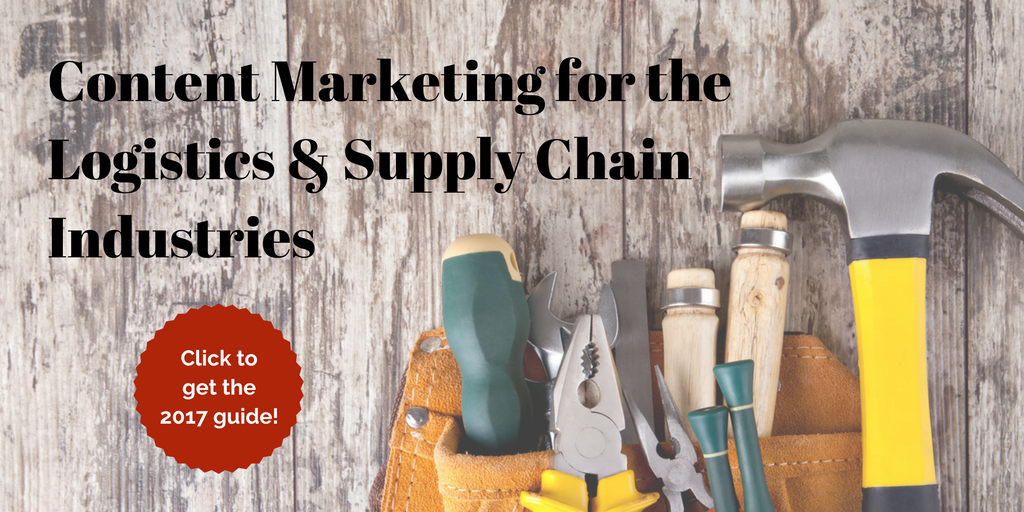
by Jennifer Hart Yim | Apr 25, 2019 | Blog, Supply Chain, Talent
New research backs up what we already know: the supply chain economy is a hotbed of innovation, and that opens up immense professional opportunities.
Highlights:
- New research assigns some numbers to two facts that every Supply Chain professional knows: the sector is full of opportunity for professionals and it is a hotbed for innovation.
- Supply Chain industry innovations have a tendency to reverberate and cascade throughout the wider economy as they filter from suppliers, to the companies they supply, and finally to the consumer.
- People who are able to harness and drive supply chain innovation have some of the brightest job prospects in tomorrow’s economy.
This guest post comes to us from Argentus Supply Chain Recruiting, a boutique recruitment firm specializing in Supply Chain Management and Procurement.
A new Harvard Business Review article lays out some striking research out of MIT about the role of Supply Chain Management within the broader economy. Written by Mercedes Delgado and Karen Mills, the study seeks to better define what constitutes the “Supply Chain” part of the economy, and what doesn’t. The goal? To better define Supply Chain Management’s place in the broader economy, and the role it plays in terms of innovation.
The researchers define “Supply Chain” industries as any industries that sell upstream to businesses and government entities. It excludes industries selling direct to consumer (B2C). It’s a bit of a curious definition – what about the B2C companies with strong supply chain and distribution networks? – but we’ll roll with it.
In short, the research assigns some numbers to two facts that every Supply Chain professional knows: the sector is full of opportunity for professionals. It’s also a hotbed for innovation which has a tendency to filter into other sectors of the economy.
The MIT researchers studied the historical role that these Supply Chain companies have played in American innovation. For example, Intel’s semiconductors and Microsoft’s enterprise software are innovations with their roots in the supply chain – supplying to companies – that are almost unparalleled in terms of their downstream effect on the overall economy, as well as the daily experience of the average person.
The researchers make an interesting point: compared to “B2C” industries, Supply Chain industry innovations have a tendency to reverberate and cascade throughout the wider economy as they filter from suppliers, to the companies they supply, and finally to the consumer. Technologies like cloud computing –which is now sold to 90% of industries – have their roots in the Supply Chain, which helps them diffuse across industries as they spread downstream and become integral to the economy. In Delgado and Mills’ estimation, this “trickling down” gives these innovations a multiplying effect that isn’t found in more consumer-facing industries.
Put aside the fact that the most successful consumer-facing companies of the past several decades have been tremendously innovative (Apple and Amazon, for example) – in part because of their Supply Chain practices – and it’s an intriguing idea. The fact is, Supply Chain management drives innovation, and the people who drive that innovation have some of the brightest job prospects out of anyone in the economy.
People in Supply Chain are more likely to be in STEM (Science, Technology, Engineering and Math) than the wider economy. They’re also better compensated – perhaps as an indirect result of their contributions to innovation.
Here are a few of the most interesting – and exciting – top-level stats from the research:
- In the U.S. – which the study examined – 44 million jobs are in Supply Chain, or 37% of the overall economy.
- The average wage of Supply Chain-related jobs was much higher than average, at $61,700 – compared to $39,200 for non-Supply Chain jobs.
- 4% of Supply Chain jobs were STEM-related jobs – considered a predictor of innovation – compared to only 2.1% of non-Supply Chain jobs.
- 6% of new patents in the U.S. evolve from the Supply Chain sector.
The researchers chart another interesting distinction and trend, towards the importance of Supply Chain Services from traditional manufacturing. Supply Chain services jobs – including logistics, engineering, cloud computing, and others – have grown massively to encompass 80% of jobs in the sector, but most still consider Supply Chain to mean traditional manufacturing jobs such as metal stamping or injection molding operators.
Supply Chain Services workers have the highest STEM intensity out of everyone in the economy (19%), which also coincides with the highest wages ($80,800 a year, on average). This tracks with a trend in the wider economy towards services and away from traditional manufacturing, and shows what we know to be the case: despite panic about automation, Supply Chain professionals who can innovate are in very high demand.
Whether you agree or disagree with Mills and Delgado’s definitions and findings, it’s clear to anyone paying attention that the Supply Chain is a force-multiplier for innovation to the economy. It’s truer now than it’s ever been, and people who are able to harness and drive that innovation have some of the brightest job prospects in tomorrow’s economy.
Do you agree with the authors’ definition of Supply Chain? Is it too broad, not broad enough, or is it right on the money? We’re curious to hear anything else you might have to add about the importance of Supply Chain for innovation in the wider economy!
In the meantime, we encourage everyone to check out the HBR article as well as the authors’ original study, which has some fascinating insights about the role Supply Chains play in innovation.
Related posts:
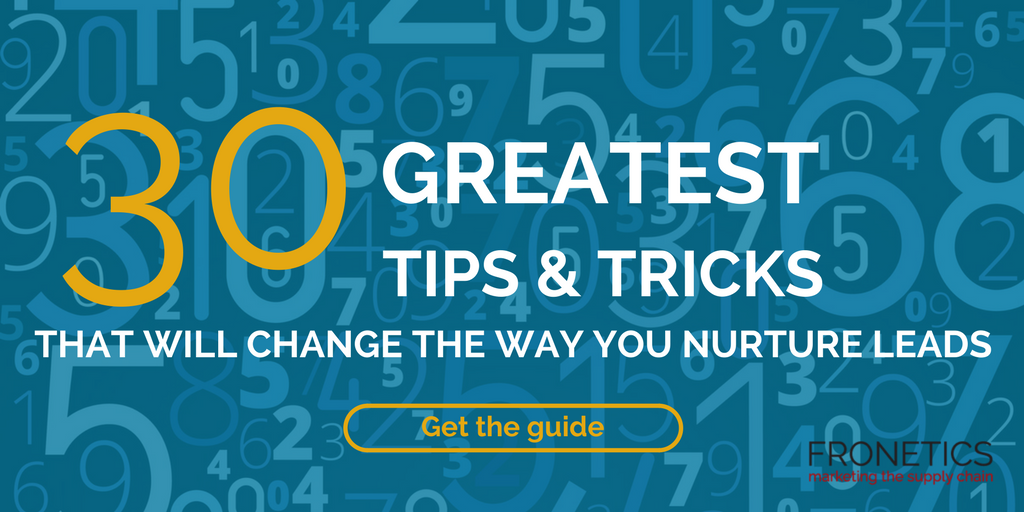
by Jennifer Hart Yim | Jan 24, 2019 | Blog, Consumer Electronics, Logistics, Supply Chain
Drones and other autonomous technology are actively being utilized in supply chains. Here’s how companies like PINC and Amazon are leveraging this new technology for inventory management.
Highlights:
- Drones and other autonomous technology are actively being utilized today in supply chains.
- PINC and Amazon are using autonomous technology for inventory management.
- By implementing new technologies, operating costs decreased by 20%, successfully boosting operating margins.
It’s been five years since Charlie Rose interviewed Amazon CEO Jeff Bezos on 60 Minutes about new innovations that Amazon was working on. Bezos revealed that Amazon was on the brink of a supply chain revolution involving octocoptor drones transporting parcels: Amazon Prime Air.
Tweets and status updates immediately conveyed consumer excitement that flying Amazon drones could deliver packages directly to doorsteps. And on the flipside, some employees of shipping carriers and brick-and-mortar retailers expressed fear that their respective industries would become obsolete.
Fast forward to the present… While advancements have been made in drone and autonomous technology, such as Amazon’s tests in the United States, Dominos’ self-driving delivery car, and Tesla’s self-driving truck, Bezos’ grand vision still remains a dream for impatient online shoppers.
That aside, drones and other autonomous technology are actively being utilized today in supply chains, and their usage extends beyond the conceived purpose of package delivery. One such use case that companies PINC and Amazon leverage this technology for is inventory management.
PINC: Aerial Inventory Robots
Less than 10% of the 250,000 warehouses and manufacturing facilities in the United States utilize automated storage and retrieval systems (AS/RS) for managing their inventories. Instead, they resort to manual human labor coupled with outdated storage solutions and antiquated inventory management measures. The need for automation in the factory setting is paramount.
PINC, a top provider of yard management systems, pioneered the use of drones in warehouses. Since 2014, PINC enacted the use of flying drone technology (PINC AIR, Aerial Inventory Robots) to track assets in warehouses.
PINC AIR Hardware
These “inventory robots” leverage barcode-reader technology and roam premises in an automated fashion, ensuring efficient inventory tracking. Technically speaking, the drones are equipped with optical sensors which allows them to take pictures of barcodes and obtain information for identifying and counting inventory.
Indoor aerial drones have limited GPS capabilities compared to their outdoor counterparts, and instead rely on indoor location services software to aid in setting the devices’ “travel boundaries” within warehouses.
PINC AIR Benefits
PINC AIR saves time, money, and offers a safer alternative to traditional rolling ladders for companies wishing to upgrade their inventory management system. Businesses spend less on workers’ compensation claims by reducing on-job injury rates. Their robots operate at the leisure of the company, are 300 times faster than a human performing the same work, and possess high accuracy levels. Even a daily inventory check provides a company a plethora of data.
PINC’s aerial drones replace the clipboards and spreadsheets of inventory counts by giving companies a platform that automatically displays the needed information in real time. Businesses could use this data to answer a variety of questions such as, “How many days do certain television brands sit in stock at certain facilities during the holiday season?”
Amazon Robotics (Kiva): Robots
In 2012, Amazon acquired Kiva for $775 million, phased-in its technology in its warehouses a few years later, and formed the subsidiary Amazon Robotics. Kiva robots replaced forklifts, large conveyor systems, and other human-operated machines. They’re efficient at performing monotonous tasks that previously fatigued employees, such as carrying and stacking bins around all day.
[bctt tweet=”In 2012, Amazon acquired Kiva for $775 million, phased-in its technology in its warehouses, and formed the subsidiary Amazon Robotics. Kiva robots replaced forklifts, large conveyor systems, and other human-operated machines. ” username=”Fronetics”]
Amazon made the move to continue pursuing competitive advantage in the e-commerce space along with maintaining control of the thousands of products in their fulfillment centers.
Some of Amazon’s robotics are large, 6-ton “Robo Stow” mechanical arms that move and stack bins around the factory. Others are used for carrying, transporting, and storing merchandise up to 3,000 pounds in an orderly fashion. Using these robots to stack and transfer merchandise saves aisle space in warehouses, allowing facilities to carry more inventory, meaning customers will be able to receive their goods quicker.
But what happened to the human employees? Did Kiva’s technology truly destroy thousands of jobs within Amazon’s warehouses? Is this the part when we rage against the machine due to the “robot uprising” stealing jobs?
Put your pitchforks down. No layoffs occurred, and, instead, robots and humans began working together. Despite skeptics’ views that automation is a job disrupter, SVP of Operations at Amazon Dave Clark assured, “[…] automation increases productivity and, in some cases, demand from consumers, which ultimately creates more jobs […] Warehouse workers would continue to work in technologically rich environments.”
In fact, since the Kiva acquisition, Amazon increased the number of warehouse employees by nearly 200% to an upwards of 125,000 workers due to the increased volume of orders. Signs show no stopping either with the rising demand of high-skilled programming jobs, technicians, as well as those working hand-in-hand with robots.
Existing employees took on new roles and increased their skillset. For example, some employees moved to “stow” products on shelves for the robots to move away, following computer instructions to optimize where merchandise goes.
From there, the robots line up when customer orders arrive. Human “pickers” grab the products from the robots’ shelves and place them in plastic bins. At this point, merchandise is packed in cardboard boxes for customers. Warehouse jobs become less monotonous as the products that employees place on the robots vary.
And with that said, the cost savings from this technology is astounding…
Cost Savings → Increased Efficiency
Operating costs decreased by 20% at a $22 million savings from each fulfillment center, successfully boosting operating margins. These savings are attributed to enhancing warehouse efficiency. Amazon found that cycle times decreased between 75% and 80% to just 15 minutes. As a side effect, additional space was allocated for inventory, increasing the amount of storage by 50%.
Drawbacks & Limitations of Autonomous Technology in Supply Chains
PINC: Barcodes & Drone Power Source
PINC’s optical technology requires packages to display barcode tags in plain sight for the drones to process accurately. This raises concerns for companies who do not have this ideal setup in their warehouses, potentially raising costs.
Another issue is the drone power source. AIR drones are powered with hydrogen fuel cells instead of batteries as they last longer and charge faster. PINC CEO Matt Yearling revealed that the hydrogen-powered technology can fly up to three hours, and only needs a few minutes to refuel. Companies therefore need to strategically consider when the drones are scheduled to fly and follow-up with refueling procedures when the drones’ power is depleted.
Amazon Robotics (Kiva): Robots Cost & Limitations
The robots themselves are also limited in the tasks that they can perform. For example, the “robotic arm” was designed to pick up packages of certain sizes. Amazon has been in the process of researching their flexibility to complete more advanced tasks, though for now human workers help in that regard. After all, “There are many things humans do really well that we don’t even understand yet,” says Beth Marcus, an Amazon employee who specializes in robotics.
While autonomous technology clearly has its benefits, it comes with a cost. Aside from the initial expense Amazon incurred with Kiva’s acquisition, an installation cost of $15 million per location is required, costing Amazon nearly $1.7 billion to fully deploy robots in all 115 locations. Despite this cost, Amazon nets a savings of $7 million per facility when compared with its recurring annual savings.
Conclusion
While introducing new technology into the supply chain space is sometimes deemed as “disruptive,” the ends justify the means for autonomous technology. Along with new jobs being created, modern manufacturing workers are gaining more skills by learning to operate robots. Drones and robots allow companies to effectively match their scale and flexibility with increased consumer demand.
PINC’s drones are a great way to establish an accurate representation of inventory in real time from past to present. This further strengthens a company’s promise to fulfill needs for its customers.
Amazon Robotics enables companies to maintain incredibly efficient workflows in their warehouses and fulfillment centers.
In a poll of executives by Techpro, an astonishing 64% reported that there were no plans to leverage autonomous technology in their businesses. Applying drones and robots to inventory management gives companies a competitive advantage and a head start in taking advantage of cutting-edge technology.
It just goes to show that autonomous technology further streamlines operations and supply chains by allowing companies to reach new heights.
This article was written by Spencer Black, an MBA student at the Peter T. Paul College of Business and Economics at the University of New Hampshire, specializing in Information Systems & Business Analytics. After graduating summa cum laude from UNH in Computer Science in 2015, he has been working at Pegasystems as a Software Engineer.
Related posts:
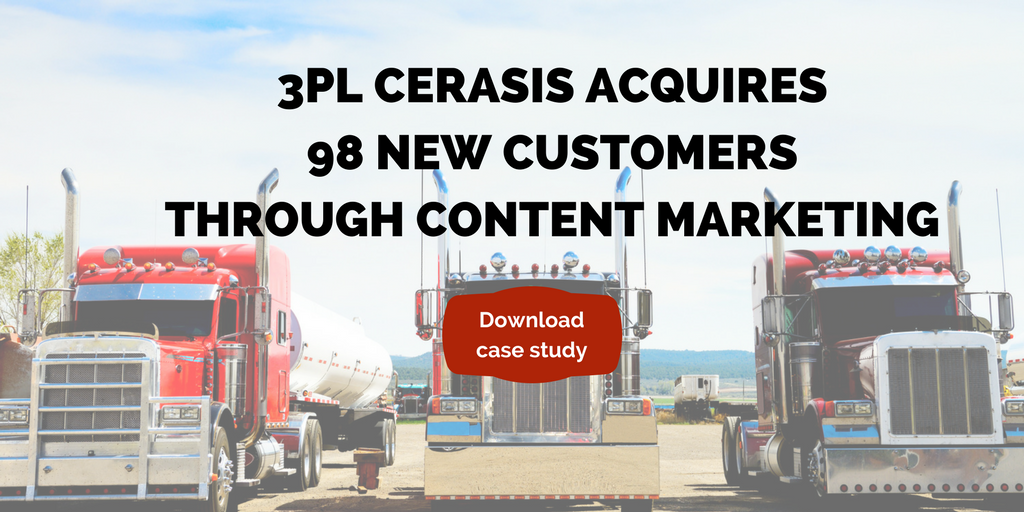
by Fronetics | Oct 31, 2018 | Blog, Content Marketing, Current Events, Marketing, Social Media
Also in social media news, October 2018: Snapchat partners with Amazon on visual search tool, Google Plus is shutting down, and Instagram adds Quick Replies for business accounts.
With the arrival of Halloween, we know that the holidays are quickly approaching. Consumers will be busy making plans and diving into holiday specials. But social networks will also be hard at work trying to stand out against brick and mortar stores as an alternative for holiday preparations.
[bctt tweet=”Businesses looking to gain traction during the holiday season will reap the benefits of social networks, which are including new features and updates that will help brands connect with new (and existing) users.” username=”Fronetics”]
Businesses looking to gain traction during the holiday season will reap the benefits of social networks, which are including new features and updates that will help brands connect with new (and existing) users. With a heavy focus on customer engagement, these new options help businesses stay connected with new features like Quick Replies on Instagram. These small but helpful updates will allow companies to have a greater reach without extra work for their marketers.
Here’s your social media news for October 2018.
Instagram founders leave Facebook
Kevin Systrom, CEO, and Mike Krieger, CTO, resigned from Instagram this week amidst rumors of tension with Facebook founder and CEO, Mark Zuckerberg. “We’re planning on leaving Instagram to explore our curiosity and creativity again. Building new things requires that we step back, understand what inspires us and match that with what the world needs; that’s what we plan to do,” writes Systrom in a statement for Instagram. Bloomberg News reports that tension between co-founders grew over the direction of Instagram. These departures create an opportunity for Facebook to oversee Instagram more directly.
LinkedIn updates Groups
LinkedIn Groups now offer more engaged conversation tools including embedded videos, images, and updates to posts, alerts, and much more. “Over the past year, we’ve focused on bringing conversations to the forefront on LinkedIn, adding new features to make it easy for you to talk to your professional communities. The new Groups experience helps you take advantage of all these conversations tools with a seamless, faster experience so you can easily participate in your groups,” writes Mitali Pattnaik for LinkedIn’s blog. All groups are currently being updated with these features.
Snapchat Partners with Amazon on visual search tool
Snapchat users are going to have a new way to search for products on Amazon, one of the world’s biggest e-commerce corporations. Using the Snapchat app, users can point their camera at a product or barcode and, once recognized, a link will appear to that product (or a similar one) on Amazon. Though the update is currently only available to a small group of users, Snapchat is hoping to roll out the new feature to all users shortly.
Instagram rolls out Quick Replies for business accounts in direct messenger
Instagram introduced Quick Replies for business accounts in direct messenger this month. The new feature allows businesses to create quick responses to frequently asked questions, like shipping rates and contact information. Quick Replies will help businesses communicate quickly and efficiently with users. Instagram tested the new functionality back in May, but just made the update available on all devices and the web.
Google Plus shuts down
Google Plus, Google’s social network, is shutting down for good after a security breach that exposed up to 500,000 users between 2015 and 2018. Ben Smith, Google’s vice president of engineering, acknowledged that Google detected a security issue back in March, but immediately addressed it. In a blog post on October 8, Smith writes, “A review did highlight the significant challenges in creating and maintaining a successful Google+ that meets consumers’ expectations. Given these challenges and the very low usage of the consumer version of Google+, we decided to sunset the consumer version of Google+. “
Related posts:
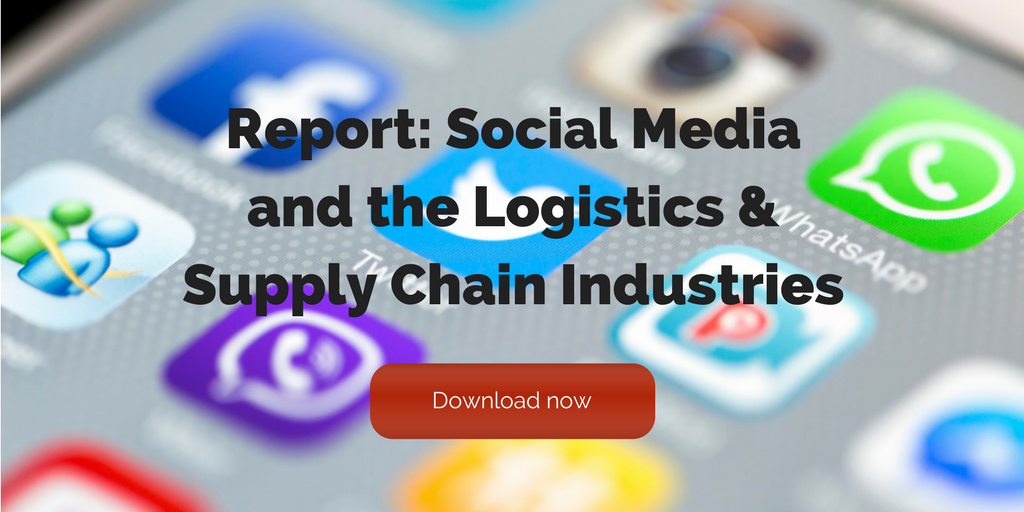